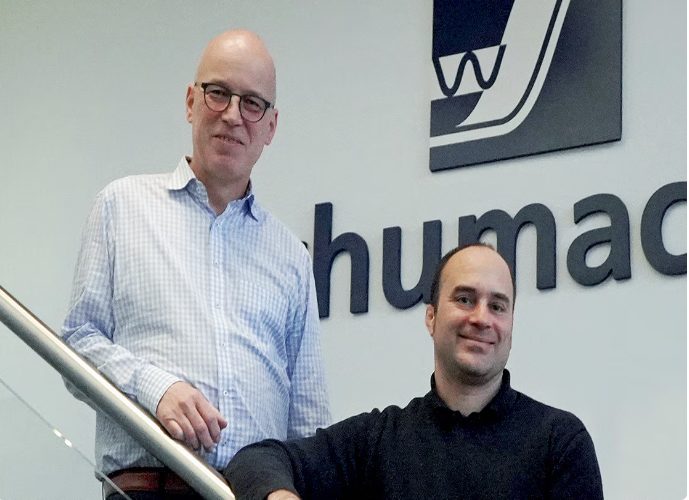
Schumacher Packaging produit une large gamme d’emballages en carton ondulé et en carton compact pour des clients de toute l’industrie. L’entreprise allemande fait appel à la version e-commerce de la plieuse-colleuse BOBST EXPERTFOLD 110 pour produire des emballages d’expédition répondant aux exigences du marché dans l’ensemble de l’Europe.
Fondé en 1948, le groupe Schumacher Packaging a son siège social à Ebersdorf, en Allemagne. Il est l’un des plus grands fabricants européens d’emballages sur mesure en carton ondulé et en carton compact. Hendrik et Björn Schumacher sont la troisième génération à diriger cette entreprise familiale, qui compte au total 29 sites de production en Allemagne, en Pologne, en République tchèque, en Grande-Bretagne et aux Pays-Bas.
La société a récemment installé deux machines EXPERTFOLD 110 e-commerce dans chacune de ses usines de production à Hauenstein et Schwarzenberg. « Ces plieuses-colleuses sont des machines extrêmement flexibles et performantes qui fonctionnent en trois équipes, 24 heures sur 24, cinq jours par semaine. Grâce à nos plieuses-colleuses EXPERTFOLD 110, il est facile de passer du carton compact au carton ondulé. Pour nous, c’est ce qui démarque les machines BOBST de la concurrence », explique Hendrik Schumacher, associé directeur de Schumacher Packaging GmbH.
La version e-commerce présente deux caractéristiques qui la distinguent du modèle standard. Elle possède tout d’abord un module GYROBOX qui permet de faire pivoter les poses jusqu’à 180° dans n’importe quelle direction entre deux opérations de pliage. Deuxièmement, la distance parcourue par les boîtes entre le collage et la réception est plus longue. Cela permet à la colle de sécher correctement , même à des vitesses de machine élevées. Les points de colle garantissent ainsi aux boîtes la stabilité requise.
GYROBOX améliore la fiabilité
« Depuis quelques années, la demande d’emballages nécessitant une rotation de 90° pendant le processus de pliage-collage est en hausse. C’est la raison pour laquelle nous avons décidé de passer au système BOBST GYROBOX il y a quatre ans », explique Hendrik Schumacher.
Auparavant, les poses heurtaient une barre d’arrêt avant d’être tournées. Cette approche standard présente toutefois un inconvénient majeur : plus les machines tournent vite, plus les poses heurtent la butée mécanique. « Plus le matériau est léger et plus la vitesse est élevée, moins le processus mécanique est fiable », explique M. Schumacher.
Le module GYROBOX, quant à lui, fait tourner la pose avec une précision absolue sans arrêter le flux des boîtes. Hendrik Schumacher : « Le module rotatif BOBST assure un mouvement régulier du flux de boîtes dans toute la machine. Le résultat : un processus de pliage-collage mieux contrôlé, moins sujet aux perturbations. C’est pourquoi nous pouvons faire fonctionner nos machines à des vitesses plus élevées, ce qui permet d’accroître considérablement la productivité. Cela signifie également que nous sommes moins dépendants des grammages du support et de la rigidité des poses. »
Une productivité pratiquement doublée
Un autre avantage concerne l’installation extrêmement rapide des machines, y compris du module GYROBOX. « Elle n’exige que quelques minutes. Après un changement, la qualité reste tout aussi élevée, qu’il s’agisse d’emballages en carton compact ou en carton ondulé », explique M. Schumacher en décrivant la continuité du processus.
Une fois la machine configurée, l’entreprise obtient rapidement un autre travail vendable. Pour un transformateur d’emballage actif dans les deux industries, cela représente un avantage considérable. Les machines EXPERTFOLD 110 produisent une vaste gamme de cycles de production à des prix compétitifs. En commençant par des quantités d’environ 3 000 boîtes, il n’y a pratiquement aucune limite maximale.
Hendrik Schumacher explique comment la productivité a presque doublé : « Lorsque les poses devaient être tournées pendant le processus de pliage-collage, nous réussissions à produire jusqu’à 120 000 boîtes par équipe. Avec les nouvelles machines, la production nette s’élève à 200 000 boîtes par équipe », déclare M. Schumacher, qui explique que la productivité a pratiquement doublé.
En outre, la plus grande distance entre le processus de collage et celui d’emballage permet à la machine de fonctionner plus rapidement tout en rendant l’emballage des boîtes moins contraignant. La distance supplémentaire parcourue avant l’emballage signifie également que cette étape de travail est plus silencieuse. Hendrik Schumacher : « Il en va de même pour le processus de pliage : plus la distance est longue, plus les machines ont de temps pour plier les rabats des boîtes. Ceci améliore la qualité du produit final.
Flexibilité et développement durable
L’entreprise utilise les versions e-commerce de l’EXPERTFOLD 110 pour fabriquer des enveloppes d’expédition en carton compact, des conteneurs d’expédition en carton ondulé et des variantes d’emballage collées en trois points. « Nous sommes en mesure de produire des emballages complexes à l’aide d’un collage spécialisé et des boîtes standard avec une base, un couvercle et des rubans auto-adhésifs. Cela facilite la vie de nos clients, car il n’est pas nécessaire d’utiliser du ruban adhésif pour sceller les boîtes. La simplicité de gestion de l’emballage est essentielle à leurs yeux. »
La production d’emballages performants en un seul passage de la machine et le doublement de la productivité de la ligne de pliage-collage permettent de réduire la consommation d’énergie par boîte. Dans l’ensemble, le processus de production et l’emballage individuel ont gagné en durabilité. En outre, les déchets ont été réduits de 50 %. L’équilibre environnemental du processus et la durabilité des produits d’emballage individuels sont ainsi optimisés.
Hendrik Schumacher : « Nos opérateurs de machines peuvent obtenir une disponibilité maximale de l’EXPERTFOLD 110 en toute simplicté. La technologie BOBST est mature et robuste. Nous l’avons vraiment mise à l’épreuve, mais elle ne nous a jamais déçue », conclut Hendrik Schumacher.